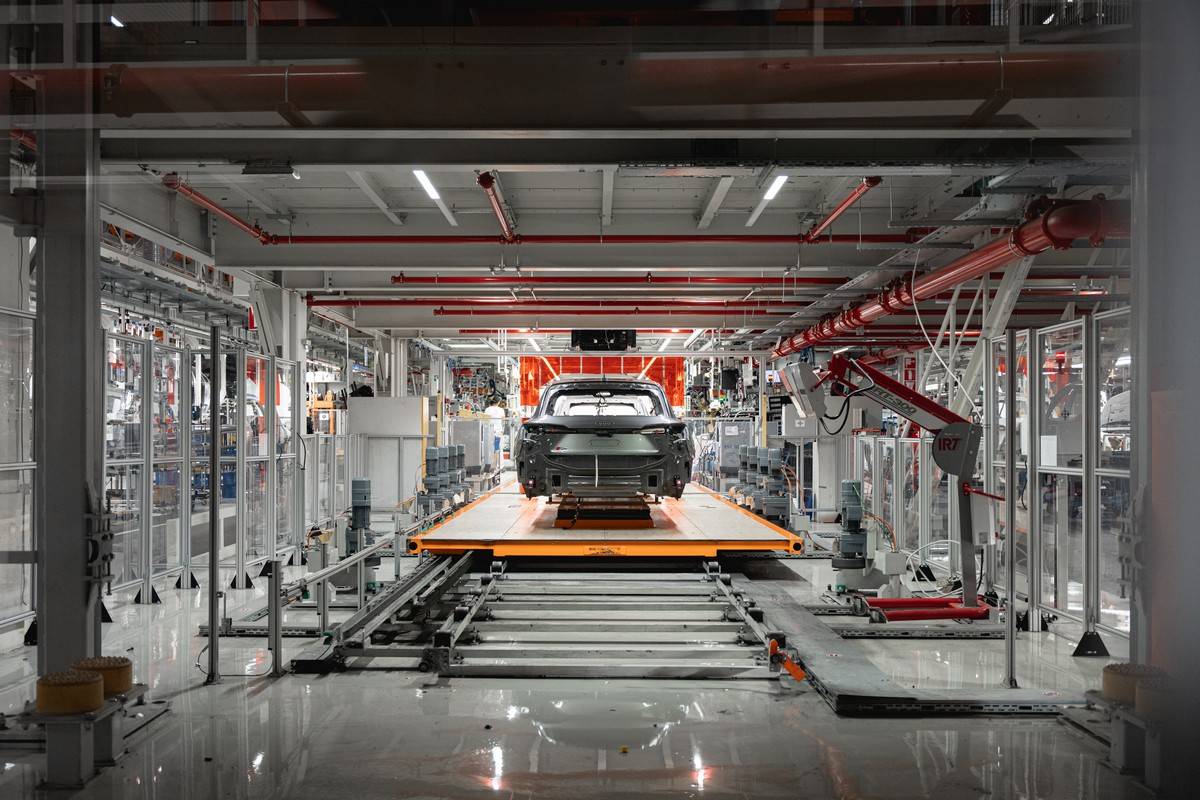
A soli sei chilometri dalla Grand Place, il centro pulsante della città di Bruxelles, capitale del Belgio, sorge un sito che è un fiore all'occhiello dell'industria automobilistica europea. Questa non è una fabbrica come tutte le altre, ma il primo impianto di produzione a grandi volumi certificato a zero emissioni di CO2 al mondo, nel segmento premium. Qui, in quest'area che veniva chiamata la foresta, Audi ha un quartier generale strategico, collegato perfettamente a una grande arteria autostradale e a un dedalo di binari ferroviari funzionali e dedicati (si entra ed esce dagli hangar della fabbrica con il treno), dove oggi si produce una delle punte di diamante della gamma dei Quattro Anelli: la Q8 e-tron. Il grande SUV, sportivo e sofisticato, nasce in questo stabilimento che, solo fino a pochi anni fa, era la casa della piccola A1. La grande rivoluzione intrapresa dal colosso tedesco nel 2016 ha permesso di avere oggi un verde polmone produttivo, che dà lavoro a più di 2900 persone.
Tra passato e presente della fabbrica di Bruxelles
Le origini di questa fabbrica affondano le proprie radici in un passato molto lontano. Nel 1948, in un'Europa segnata inevitabilmente dalla devastazione della Seconda Guerra Mondiale, l'americana Studebaker investe in Belgio e realizza la fabbrica di Bruxelles, che all'epoca contava su 12.000 metri quadrati. L'anno seguente è già tempo di festeggiare il primo veicolo prodotto, una Champion Sedane, che strega tutti quanti con la sua linea massiccia e voluminosa, come andava di moda oltreoceano. Nel 1948, la Volkswagen si affaccia timidamente tra le catene di montaggio della capitale belga, con il suo Maggiolino e il Transporter T1, la prima generazione del van più famoso al mondo. Strada facendo il costruttore di Wolfsburg aumenta la propria presenza, fino a diventare il primo e unico interlocutore.
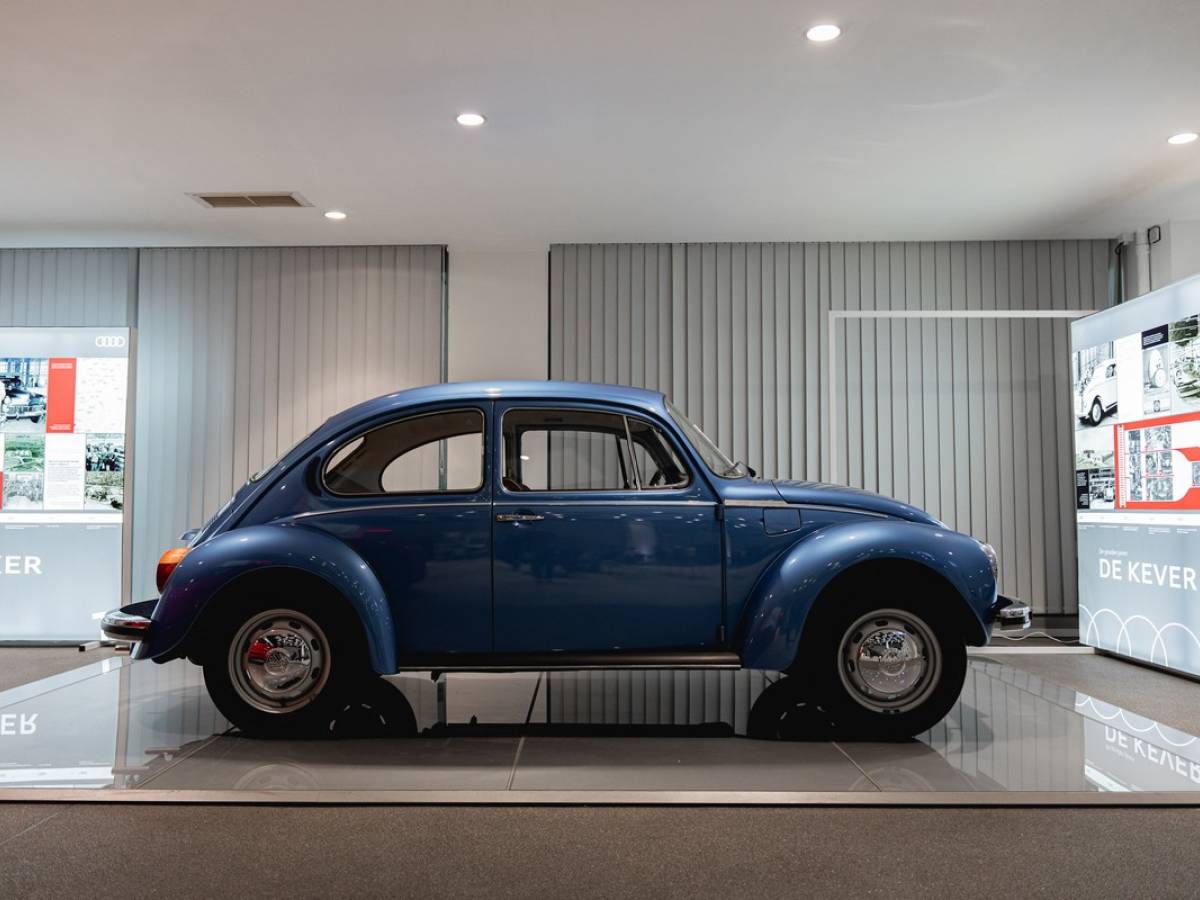
D'Ieteren, il fondatore, nel 1970 cede la sua creatura alla Volkswagen che trasformerà lo stabilimento in un cantiere attivo e dinamico, dove vengono assemblati modelli iconici come la Golf (per 5 generazioni) e la Passat (per 4 generazioni). Dopo un breve interregno di Seat, nel 2007 il sito della "Foresta" diventa un fortino di Audi, con la catena di montaggio destinata alla piccola A1 a partire dal 2010. Poi, nel 2016 viene scritto il primo capitolo della rivoluzione che si concretizza nel 2018, con il passaggio alla divisione e-tron, con i veicoli elettrici dei Quattro Anelli che qui trovano un avamposto moderno e sicuro, che analizzeremo più nel dettaglio nelle prossime righe.
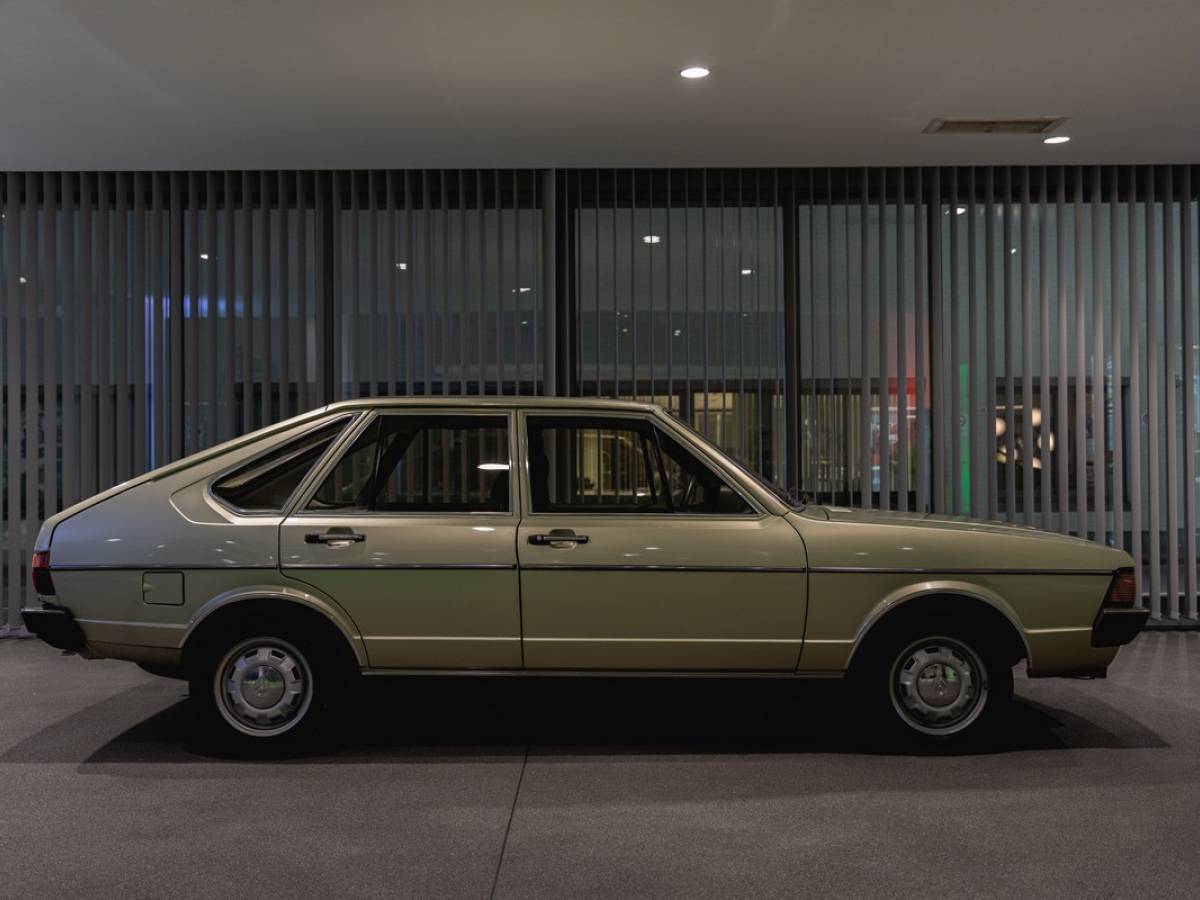
Dall'inizio della storia, dal sito di Bruxelles sono usciti oltre 8 milioni di veicoli: 750.637 sotto l'egida di D'Ieteren, 5.980.281 col marchio Volkswagen e più di 1.300.000 con l'effige di Audi; va da sé che questo numero è in continuo aggiornamento. Sono già oltre 200.000 le auto elettriche sfornate nelle capitale belga, che oggi produce per tutto il mondo (Cina esclusa poiché ha i propri siti interni) l'intera gamma Q8 e-tron, che comprende anche: Q8 Sportback e-tron, SQ8 e-tron, SQ8 Sportback e-tron. Qui, nel 2022, sono state realizzate 50.302 automobili e l'ambizione legittima è quella di crescere ancora.
All'interno del sito di Audi
Rispetto a più di settant'anni fa, la fabbrica di Bruxelles conta un'area complessiva di 563.321 metri quadrati, con una serie di padiglioni grandi come piccoli villaggi. Fra questi ci sono: la zona body shop, il paint shop, la superficie di car assembly, gli uffici di management e amministrazione, il reparto analisys e, infine, il modernissimo impianto di battery assembly. Un tempo qui si operava in modo differente, le condizioni di lavoro era più difficili con gli operai costretti ad affannarsi tra le catene di montaggio, con il frastuono dei macchinari che non permettevano mai un attimo di pace. Quell'idea di vita affannosa e stressante, come raccontano coloro che hanno visto con i propri occhi il cambiamento, è un capitolo storico ampiamente superato.
Nella fabbrica di Audi oggi si vive come in una placida oasi, dove il fracasso è stato sostituito dal sibilo dei nuovi bracci meccanici automatizzati, che si muovono in modo armonioso e che operano con una precisione chirurgica, come in una sala operatoria. La prima linea di assemblaggio è l'avamposto dove si costruiscono le culle delle batterie, qui i robot danno vita a danze frenetiche, saldando e avvitando. Si può restare ipnotizzati di fronte a questo prodigio della tecnica.
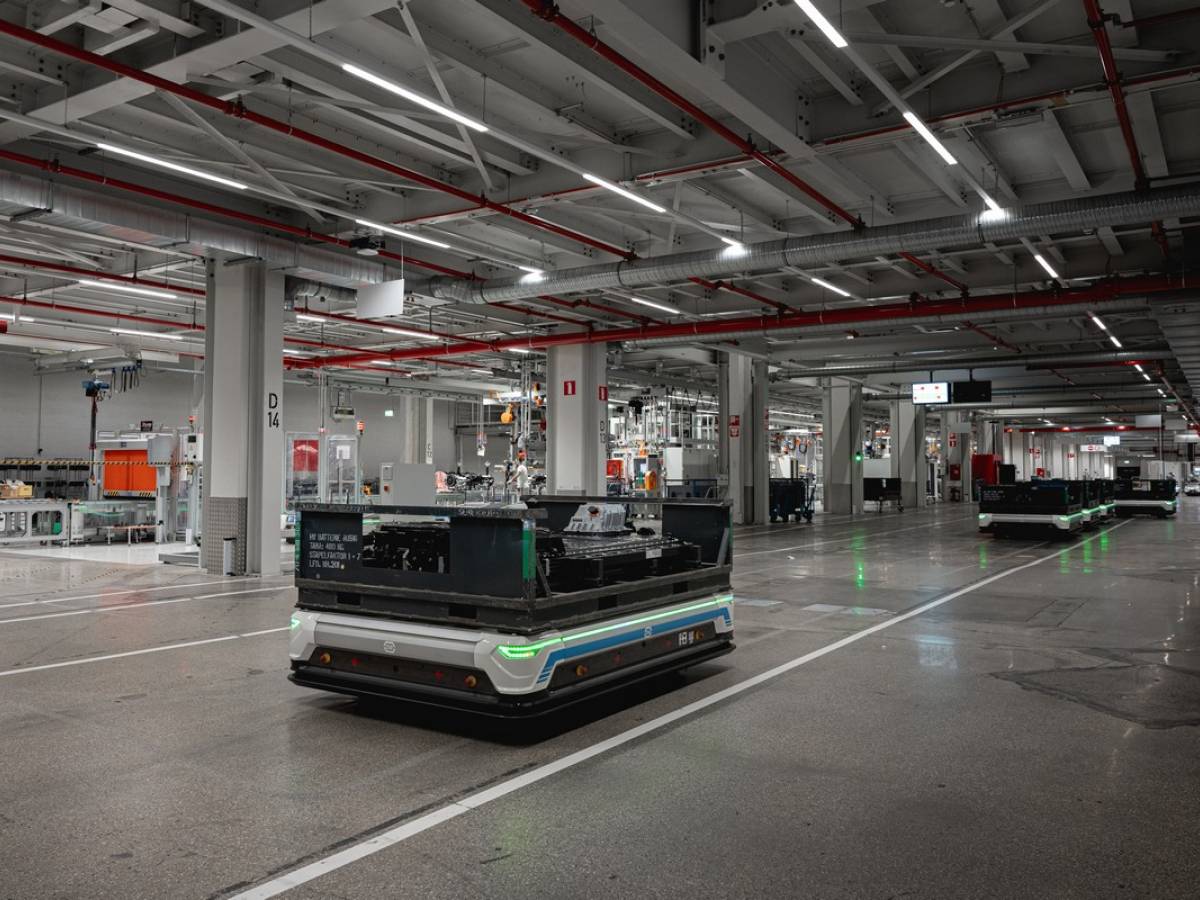
Tutto è organizzato in maniera maniacale, i tempi sono scanditi da un ordine ben preciso, che viene rispettato religiosamente da chiunque. Tanto dagli automi, quanto dagli esseri viventi. Il fattore umano è ancora determinante all'interno della fabbrica, e lo si vede nei reparti superiori, dove senza le sapienti mani e gli occhi esperti degli svariati tecnici non si potrebbero assemblare in modo così perfetto ed efficace le vetture premium dei Quattro Anelli. Certo, per chi ha visto il passaggio da un piccola auto a combustione interna a un grande SUV elettrico non è stato di certo facile.
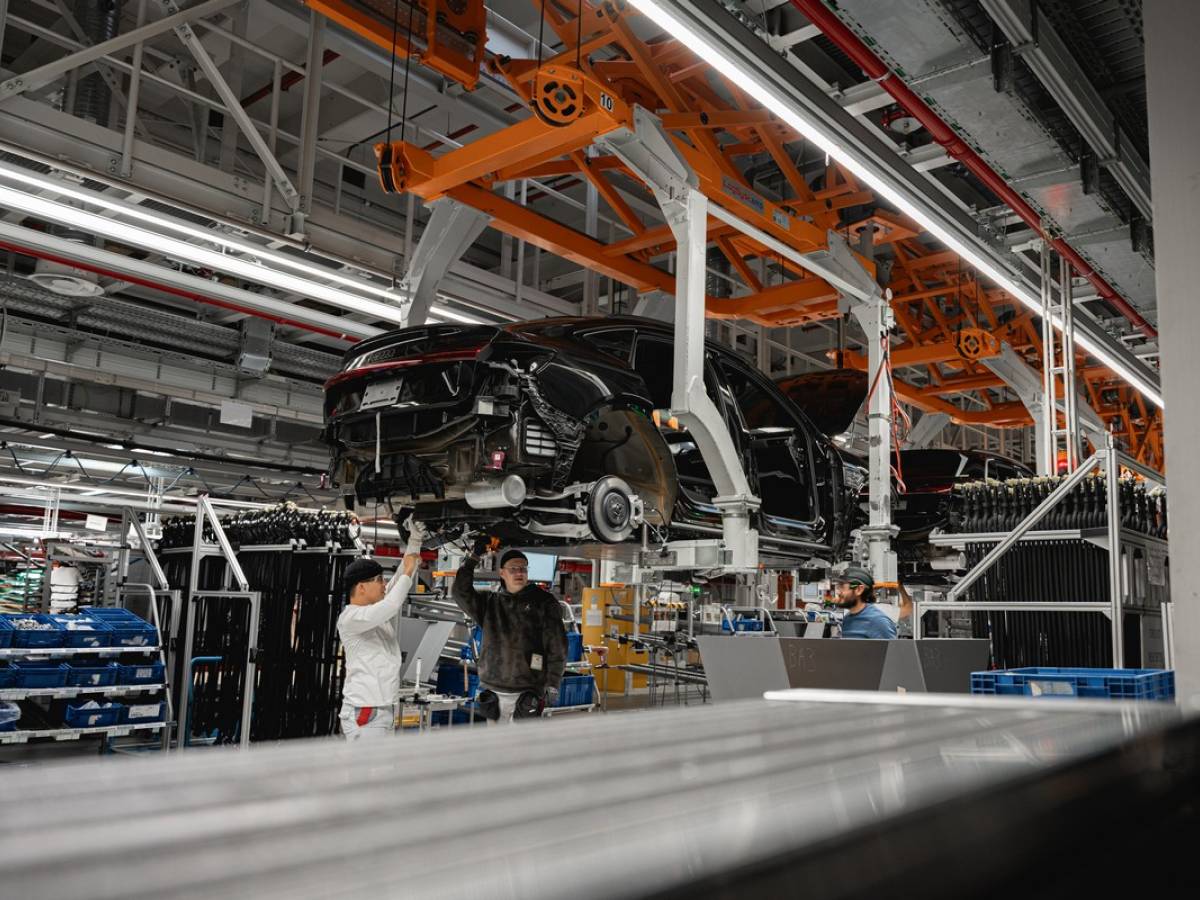
La parte finale è quella forse più suggestiva, quella che riempie maggiormente l'occhio. Le carrozzerie delle auto sembrano fluttuare nell'aria, aggrappate a forti supporti che reggono fino a 6 tonnellate di peso, per congiungersi in ciò che viene chiamato "matrimonio" con il resto della scocca e con il pacco batterie. L'alto e il basso si uniscono con una precisione assoluta, e la macchina esce da lì quasi completa. Dopo l'auto torna ad altezza uomo e viene il momento di installare i paraurti, i sedili anteriori e posteriori, e tutti gli elementi che mancano. Qui la forza lavoro segue passo passo la propria vettura, passeggiando con lei lungo il carrello che si muove lentamente, saltando dentro all'occorrenza, avvitando e finendo l'opera che è ormai prossima al compimento. In questo reparto i turni sono due e durano un paio d'ore ciascuno. L'area di tinteggiatura resta invece offlimits, ed è un peccato, ma le fibre dei tessuti esterni potrebbero depositarsi sulle vernici, vanificando il prezioso lavoro.
Il capitolo batterie
Il reparto destinato all'assemblaggio batterie è staccato dai corpi centrali e bisogna raggiungerlo con un'auto. Il viaggio dura pochissimi minuti. Al suo interno si respira l'avanguardia della tecnica, come dice il motto di Audi, ed è un tripudio di sicurezza ed efficienza. Le macchine e gli uomini lavorano all'unisono tra fili e moduli, dove spicca il colore arancione, che indica il cablaggio più pericoloso. L'obiettivo finale è la creazione di una struttura simile a un sandwich, composta da: coperchio inferiore di protezione, sistema di raffreddamento, cornice della batteria, culla, struttura di separazione in alluminio, moduli di controllo delle celle (36 moduli da 12 prismi ciascuno), coperchio e box di collegamento. L'opera conclusiva è una batteria da 700 chili con un voltaggio nominale di 396 V e una potenza di 95 kW, da installare sotto alla Q8 e-tron. E se la batteria arrivasse a fine vita, il nuovo software di analisi BattMAN ReLife controlla in pochi minuti il suo stato di salute, per destinarla a un nuovo uso.
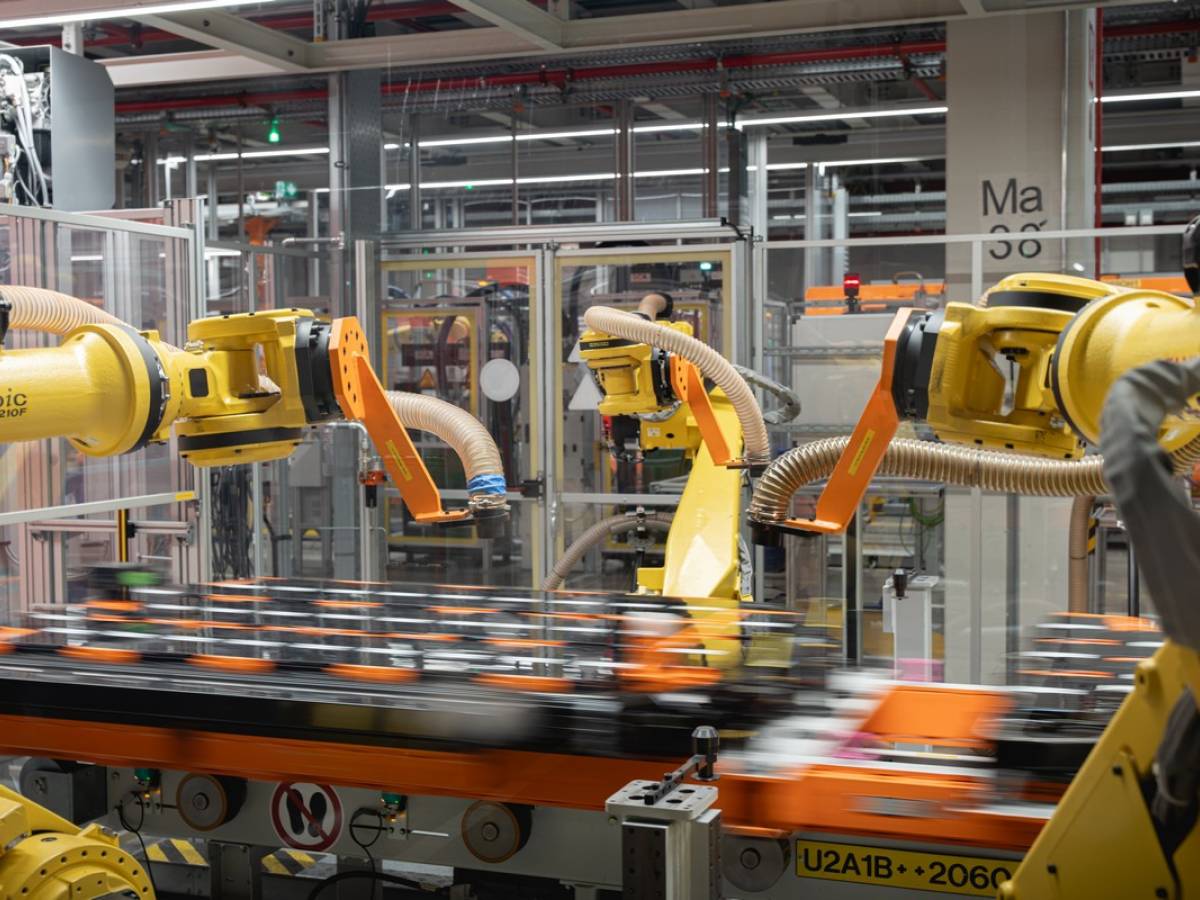
La Mission Zero
L'obiettivo intrapreso in tempi non sospetti da Audi è quello di riuscire a trasformare questo sito in uno stabilimento "Carbon Neutral" e a zero emissioni di CO2. Non è stato facile, ci è voluto del tempo, ma nel corso dell'ultimo decennio sono state apportate una lunga serie di manovre che hanno favorito il raggiungimento di questo ambizioso traguardo. La svolta green di Audi Brussels è stata possibile anche grazie alla massiccia superficie, corrispondente a 107.000 metri quadrati, destinata soltanto a impianti fotovoltaici, che sono attualmente i più grandi della regione. Ogni anno questa sistema genera circa 9.000 megawattora di energia sostenibile. Ciò è sufficiente per ricaricare circa 90.000 unità di Audi Q8 e-tron e a ridurre le emissioni di carbonio di 1.881 tonnellate.
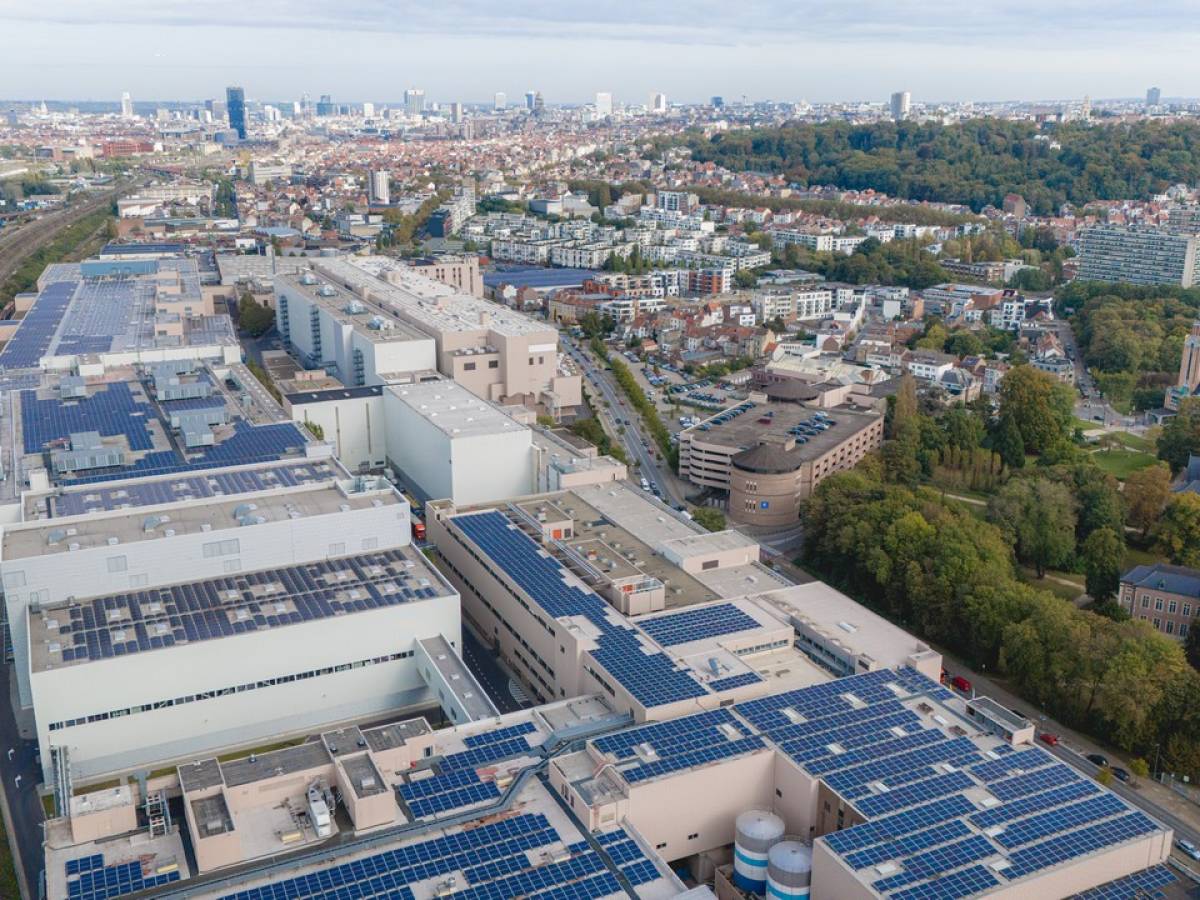
Inoltre, le aziende che forniscono le celle delle batterie sono obbligate a utilizzare solo fonti energetiche rinnovabili, mentre i motori elettrici, che vengono trasportati dagli impianti ungheresi a Bruxelles, utilizzano le linee ferroviarie. Prima, inevitabilmente, veniva sfruttata una carovana di camion, quindi un trasporto su gomma, mentre da maggio 2022 Audi utilizza quello su rotaia che si snoda su un percorso di circa 1.300 chilometri. Questa scelta ha ridotto le emissioni di carbonio di circa 2.600 tonnellate all’anno. E tutto l'ambiente ringrazia.
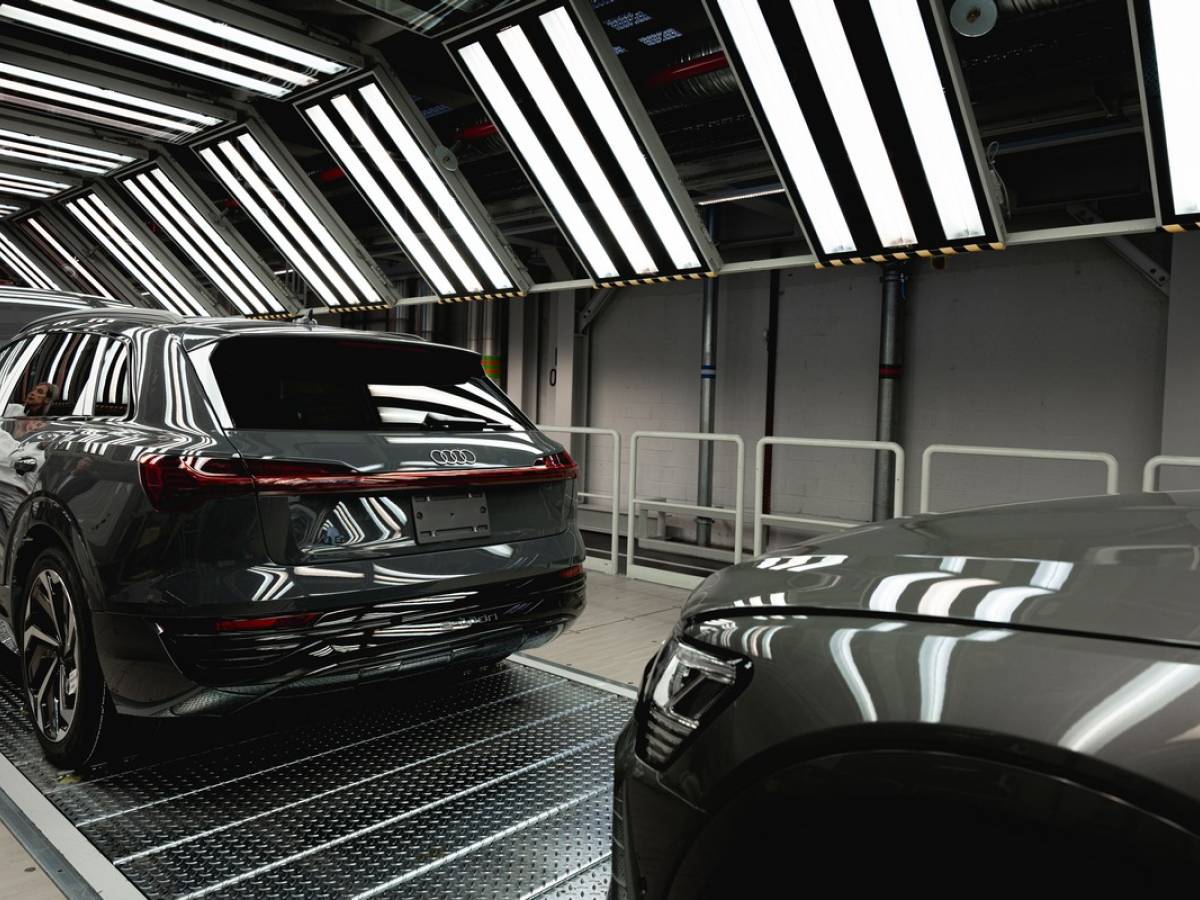
Anche l'acqua, come altre parti fondamentali del ciclo produttivo, non viene sprecata e viene riconvertita per altri usi. In prossimità della fabbrica sono presenti delle grande cisterne di h20, che forniscono il proprio apporto idrico a più di un terzo della città.
Qui, ogni anno viene ripulita una quantità di acqua corrispondente alla misura di 40 piscine olimpioniche, che può essere sfruttata in molteplici impieghi, persino domestici. L'unico stop riguarda la potabilità.